Research Thrusts
Additive Manufacturing
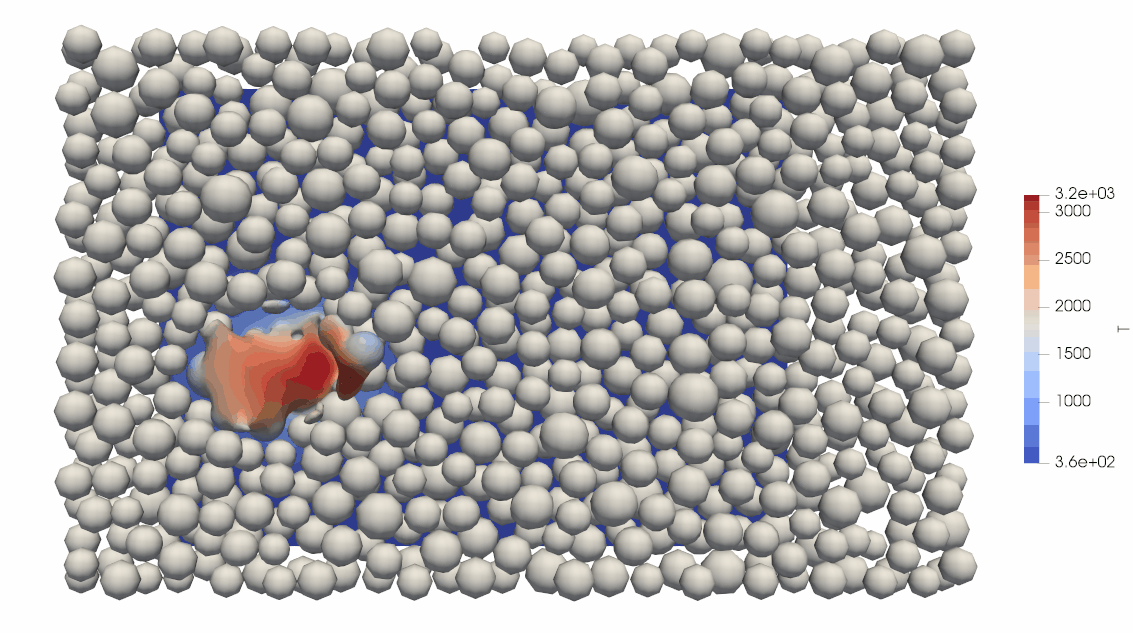
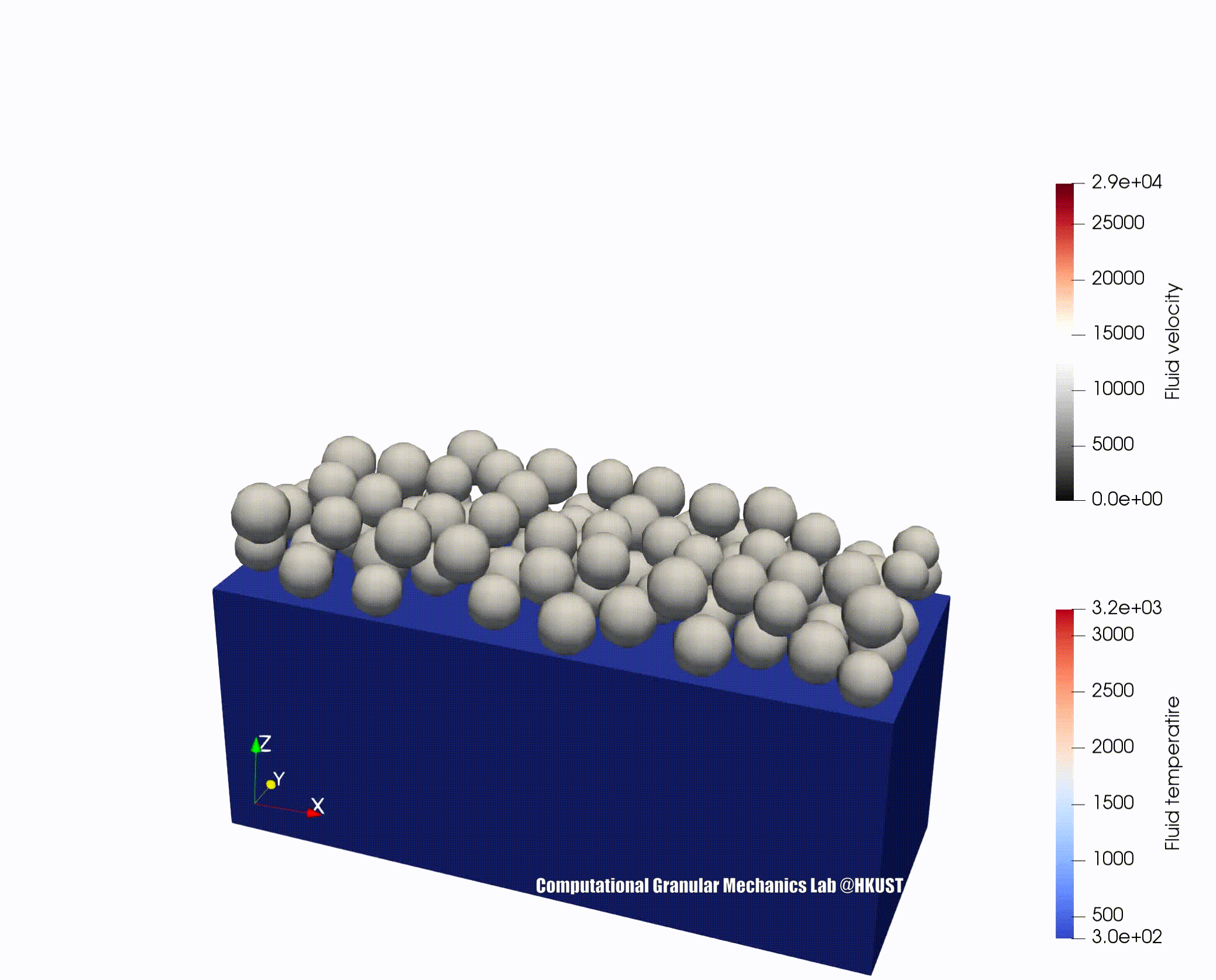
Metal Selective Laser Melting
At our Computational Granular Mechanics Lab, we aim to push the forefronts of research on granular media to any emerging areas, one of which is laser powder bed fusion (LPBF) which represents the future for metal additive manufacturing. Advance of this emerging technology is bottlenecked by the unavailability of high-fidelity prediction tools for cost-effective optiminzation of printing design. We have developed as advanced physics-based computational approach, based on rigorous coupling of fully resolved CFD and DEM to tackle the challenges featured in a typical selective laser melting process of metallic powders, including intra- and inter-phase interactions that thermal-induced phase changes such as melting, vaporization, solidification, and among others.
Our PhD student and HKPFS recipient, Tao YU, has taken the initiative in developing anew such a computational platform as an out-of-the-box extension of our previous coupled CFD-DEM simulation of debris flow and mitigation. Tao has published the methods in two papers appearing in the very top computational journal, Computer Methods in Applied Mechanics and Engineering. Please read our first paper and the more recent paper. We shall now focus on using this advanced tool to simulate key processes such as keyhole formation and pore defect to deepen our fundamental understanding of the entire laser melting process. We are committing with industrial partners for practical application of this powerful prediction tool.
Advanced Particulate Modeling
SudoDEM for non-spherical particle modeling
A new generation advanced DEM code, SudoDEM, has been developed Dr Shiwei Zhao with full function for both 2D and 3D non-spherical particles modeling. It offers a rich library of prime particle shapes, including poly-superellipsoids, superellipsoids, cylinders, cones, polyhedrons for 3D and disks and superellipses for 2D, and is further empowered by OpenMP acceleration. It features effecient contact detection algoriths to handle contacts among complex-shaped particles.
We have elected to have it open-sourced for the community to free download and use: https://sudodem.github.io. Full features of SudoDEM are summarised in a new paper published in Computer Physics Communications.
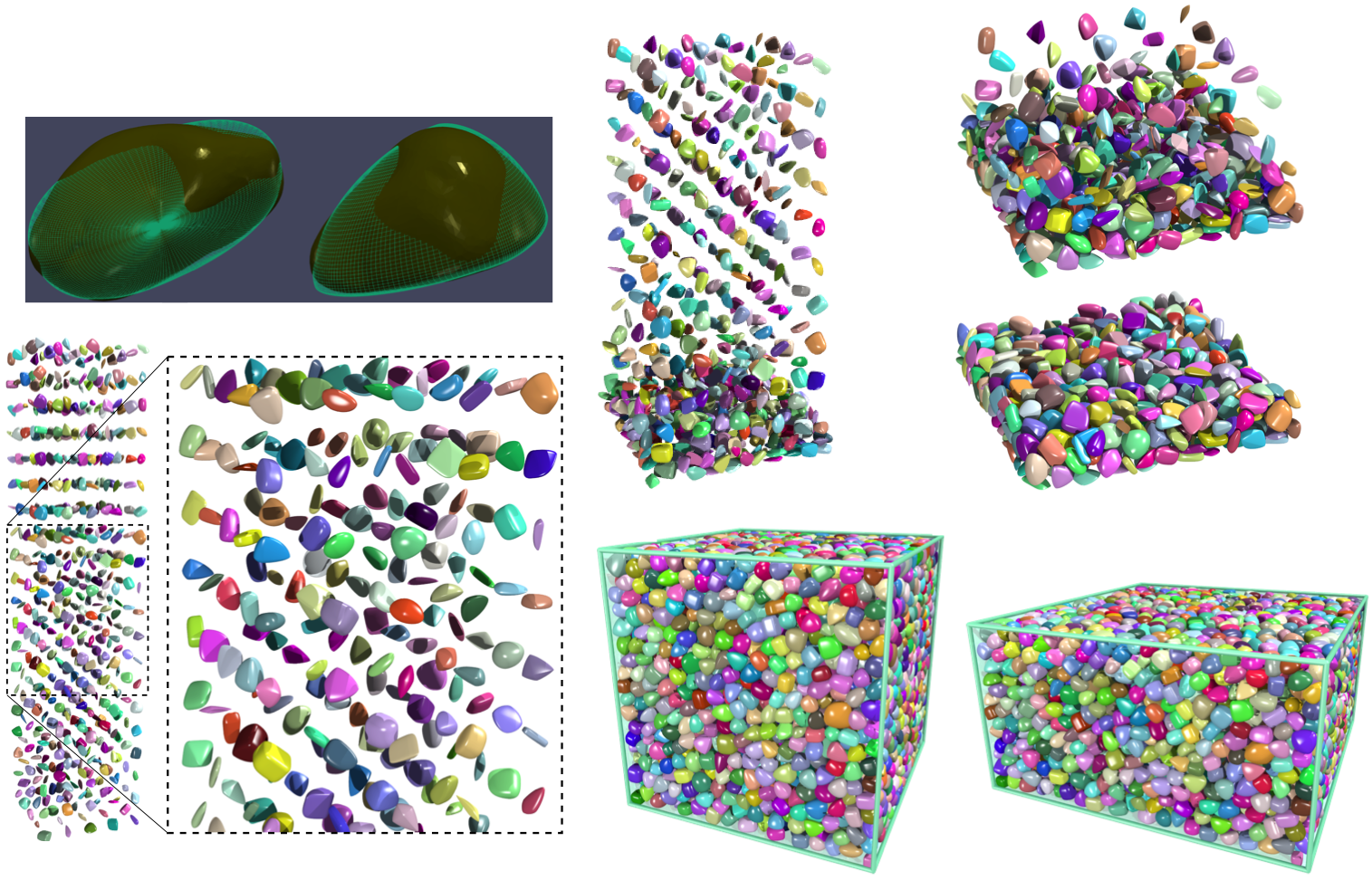
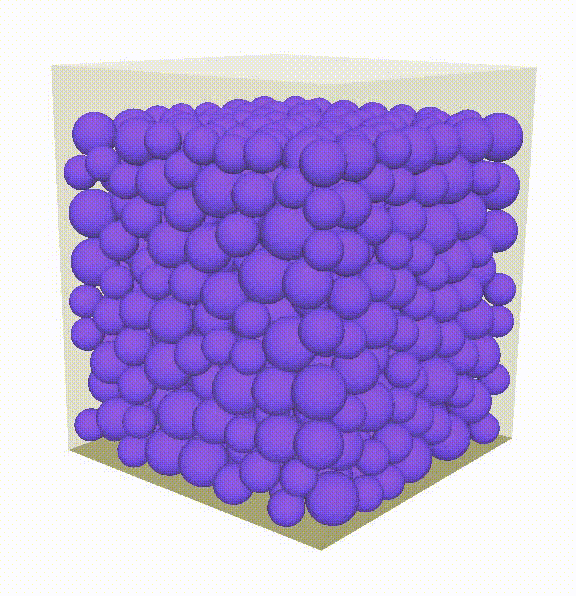
Revolutionising Simulation on Grain Crushing
Grain crushing underpins the operation and performance of applications pertaining to multiple engineering and industrial disciplines. Our Lab has developed a whole new approach to simulate grain crushing, based on hybrid Peridynamics and Physics Engine which provides more objective (crushing criteria) and realistical (shape) consideration of major aspects of the physical process of grain crushing in a context of granular packing. We use Peridynamics to treat the crushing of each individual grain, and allow Physics Engine to effectively handle irregularly shaped grains in an assembly during the crushing process (see animation of continuous crushing process in 1D compression), where the continuous evolution and interplay between grain shape and grain size apparently reflect more of the physical nature of this complicated process.
Read our recent paper published in CMAME and an earlier paper appearing in Géotechnique for details.
Rock blasting induced fractures by Peridynamics
Novel Peridynamic models have been further developed to simulate dynamic fractures caused by rock blasting. In the study we developed a new non-ordinary state-based peridynamics approach to consider pressure dependency, strain rate effect, and viscoplasticity in rock fracture under blasting, in conjunction with updated Lagrangian peridynamics with Jones-Wilkins-Lee equation of state to simulate detonation of explosives and gas expansion. For detail please reader our paper published in Journal of the Mechanics and Physics of Solids (see also PDF).
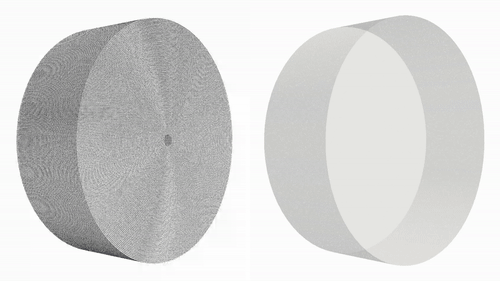
Debris Flow Mitigation by Flexible Barriers
Collaborated with government sectors, we have been engaged in developing innovative computational tools to simulate debris flow mitigation by flexible ring barrier. We coupled computational fluid dynamics (CFD) with discrete element method (DEM) to capture the multi-phase, multi-way, multi-physics interactions among the debris solids, the debris fluid and the different deformable components of the flexible ring barrier are captured, including ring-ring and ring-cable frictional contact and sliding. Read our latest paper on this subject.
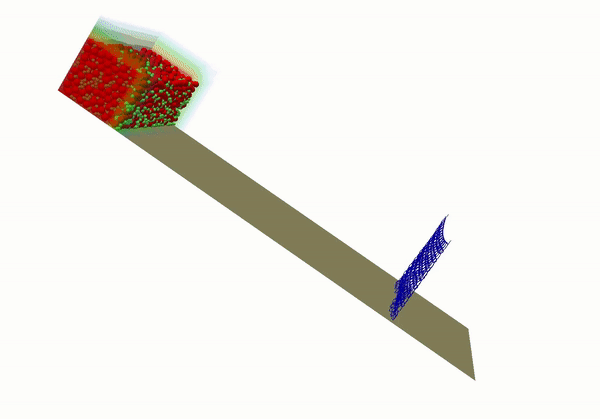
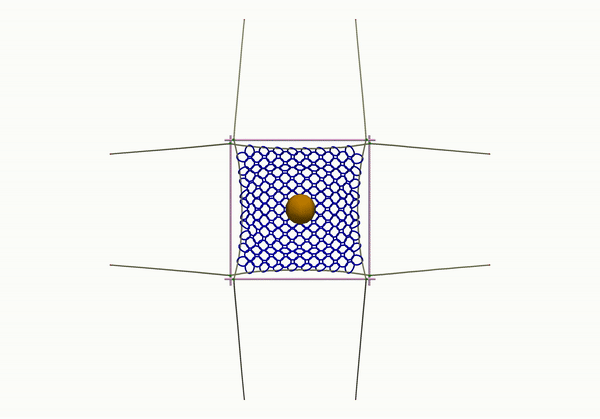
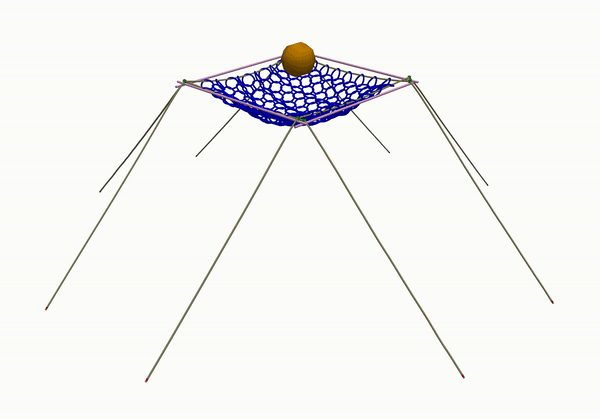
We are able to have the same ring flexible barrier subjected to the impact of different geophysical flows which may occur in a natural setting, ranging from dry rock avalanche, debris avalanche, debris flow, debris flood to mud flow, to investigate the impact mechanisms. We found that the transition from pileup to run up mechanisms is found closely related to flow features (including Froude number, solid volume concentration and fluid rheology) and barrier responses (barrier components including barrier net, cables and brakes as well as their coordinated interactions in response to the impact). The insights on the two impact mechanisms and their transitions gained in the study may provide a useful reference for future design of flexible barriers in mitigating hazardous geophysical flows. For detail please reader our paper published in Engineering Geology (see also PDF).
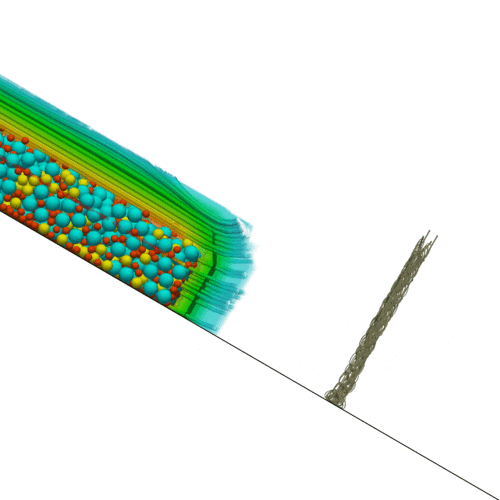
Multiscale Modeling in Geomechanics
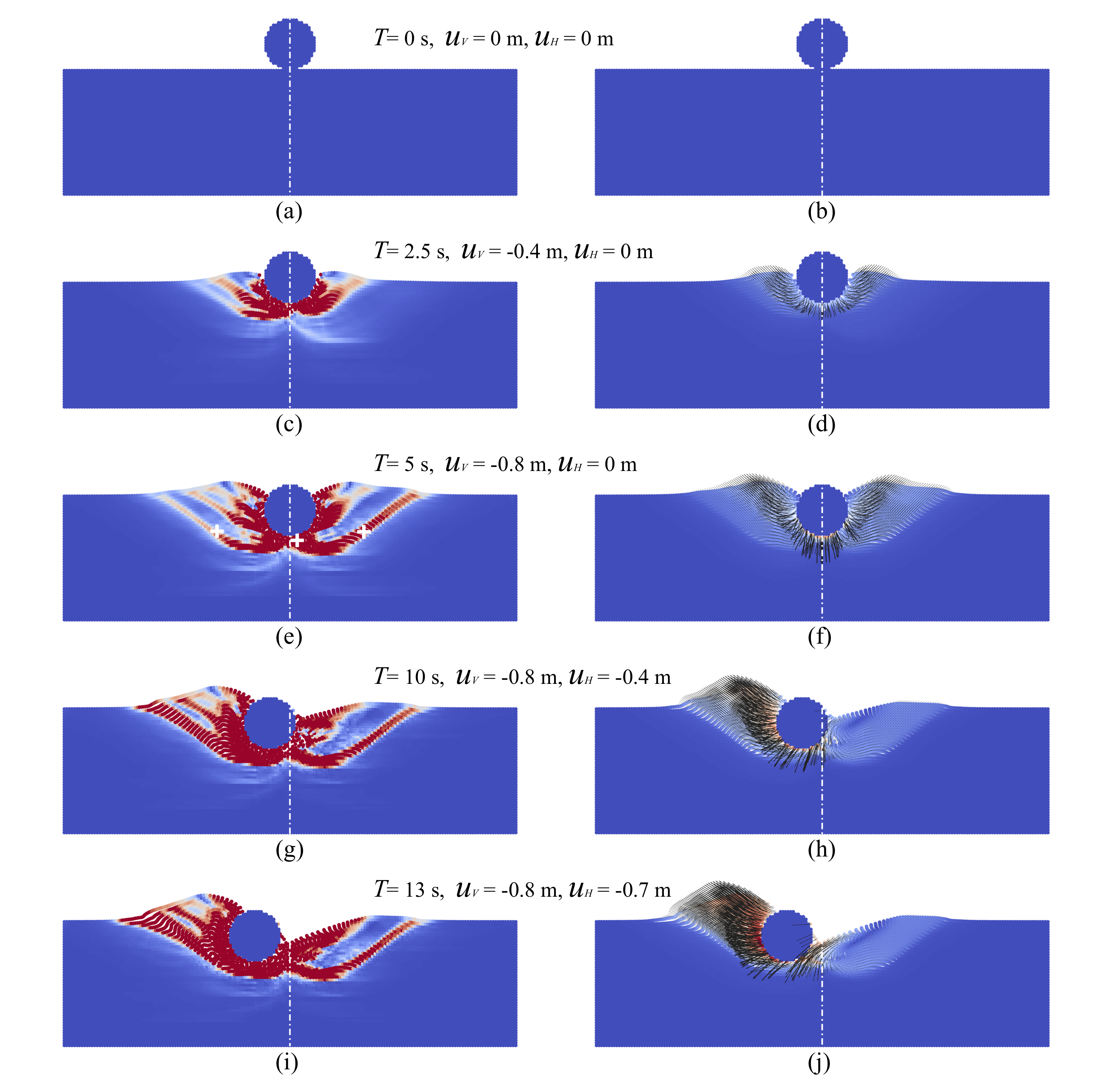
Large Deformation in Geomechanics
Our Lab has developed an innovative computational multiscale modeling framework, based upon FEM/DEM coupling or MPM/DEM coupling, to effectively tackle a wide range of geomechanics boundary value problems to offer cross-scale links between the macroscopic phenomena (such as large deformation, strain localisation, and failures) and their underlying microstructural origins and mechanisms. Large deformation failures in offshore geotechnics are a recent focus of our research (see a MPM/DEM simulation of soil-pipeline interaction in a typical seabed). Read our recent paper on this topic.
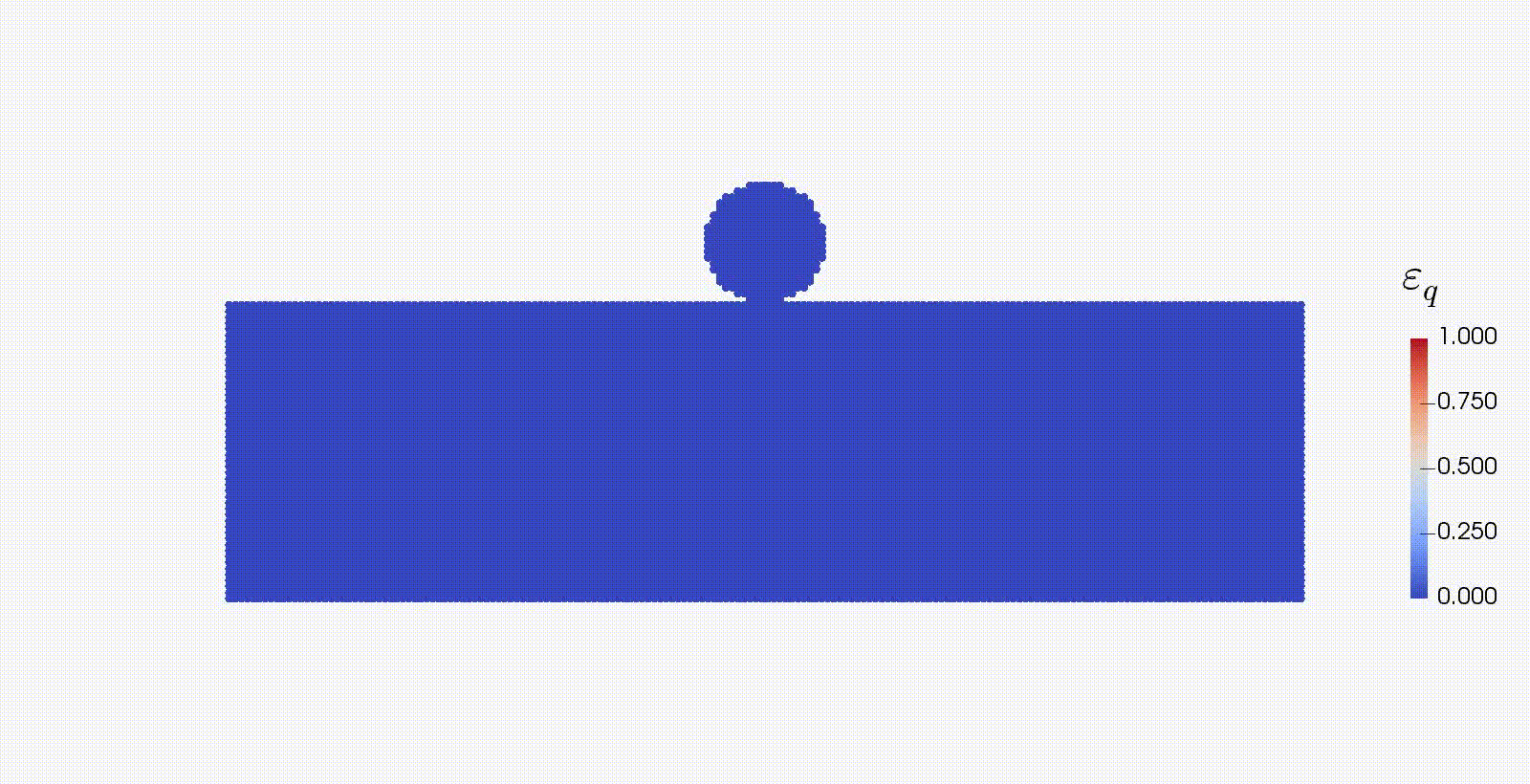
Large deformation in offshore anchor pullout
Multiscale modeling of offshore anchor pullout has been performed to predict the pullout bearing capacity of both horizontally and vertically placed anchor buried in loose and dense sand at different depth. Shown in the following animation are contact force network evolutions for three RVEs (from top to bottom) located behind and immediately in front of the anchor plate and at the edge of the front shear banding, respectively. For detail of the study refer to our paper published in JGGE (see also PDF). The work was a collaboration with Prof. Kenichi Soga of UC Berkeley.
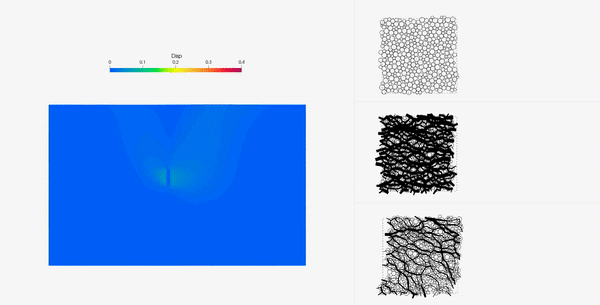
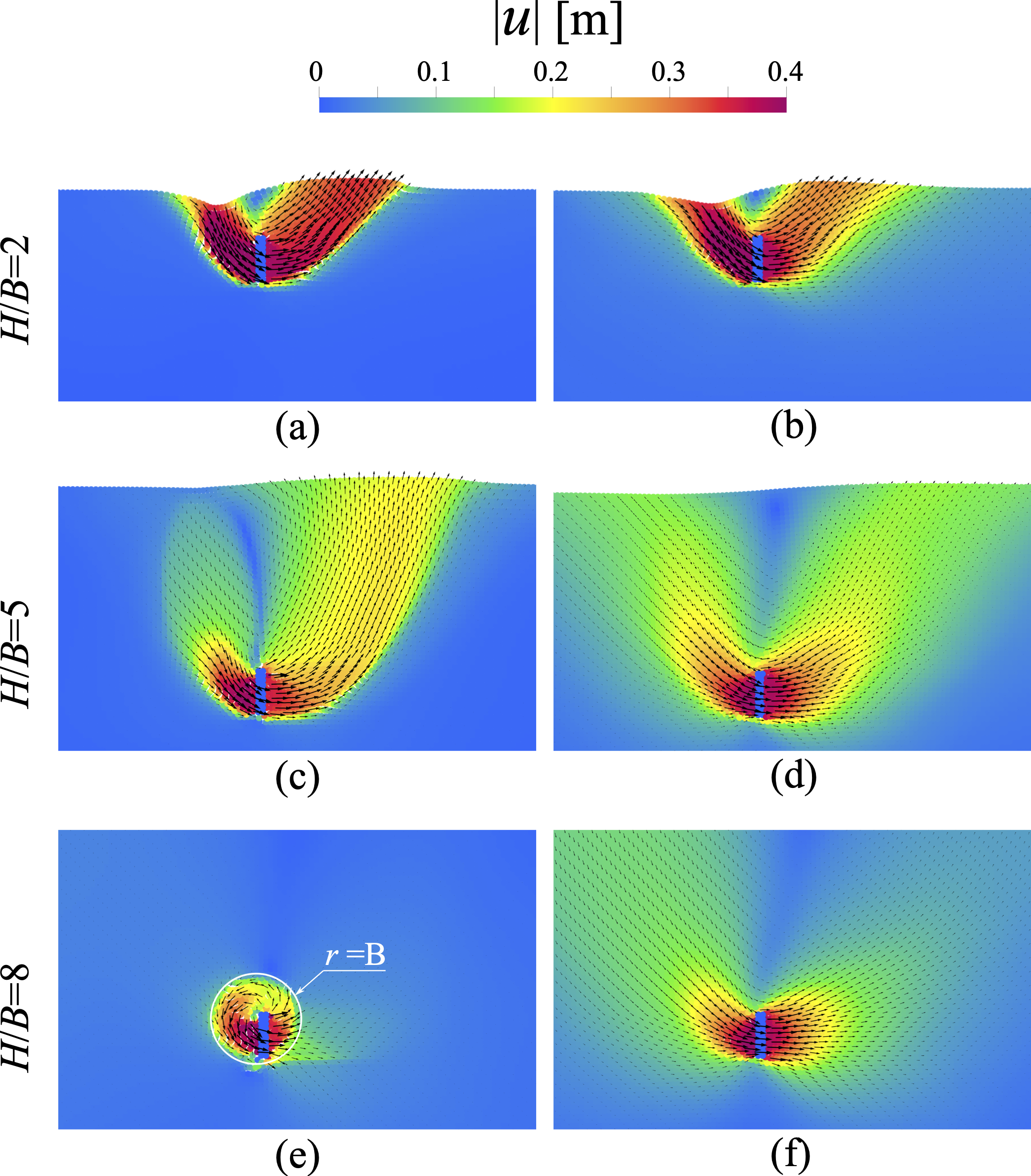
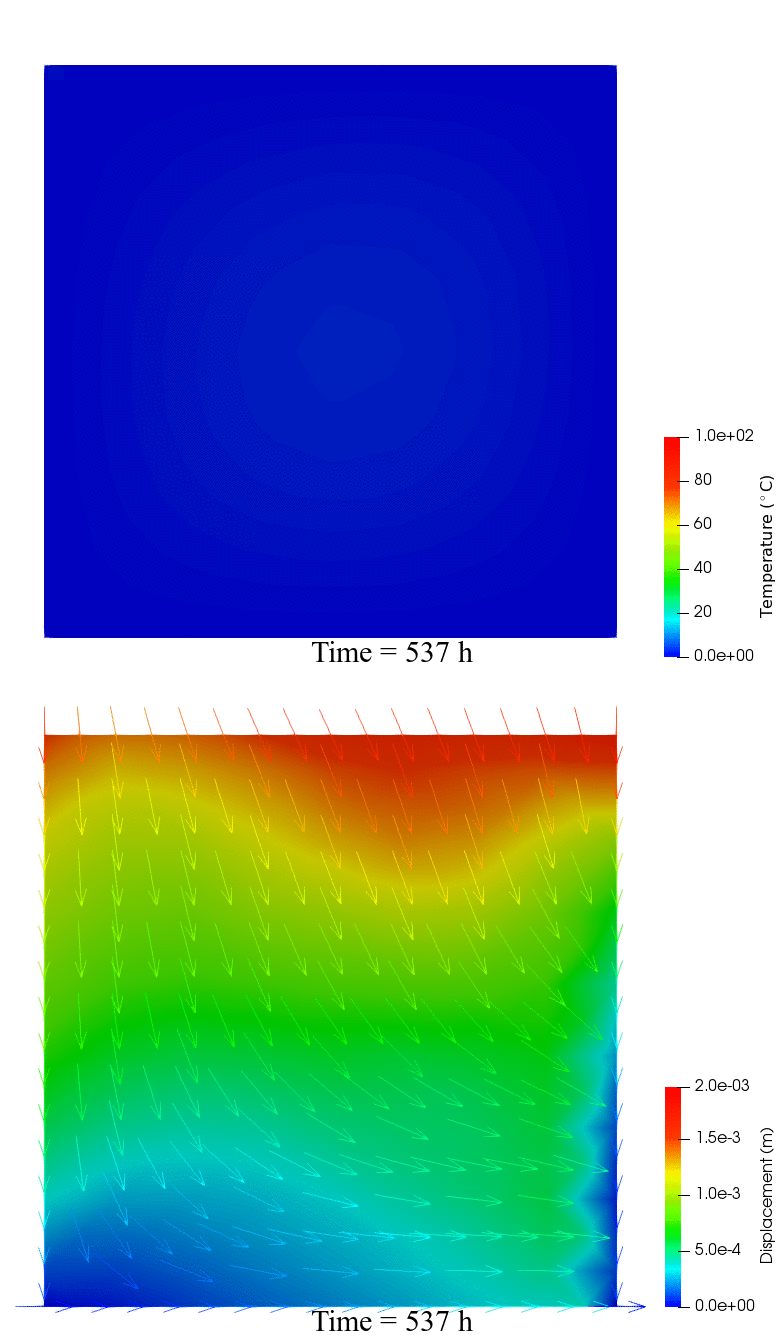
Multiscale modeling of thermo-mechanical coupling
We have further developed a novel multiscale modeling framework to simulate coupled thermo-mechanical behavior in granular media. We employ dual FEMs, one for mechanical and the other for thermal, which share common Gauss points. At each shared Gauss point, we embed a DEM assembly that considers and solve for heat conduction and force transfer at grain contacts to return required variables for the global FEM solutions. Illustrated are animations of the thermal and displacement fields for a biaxially sheared sample subjected to cyclic thermal loading.Read our paper published in Computer Methods in Applied Mechanics and Engineering.
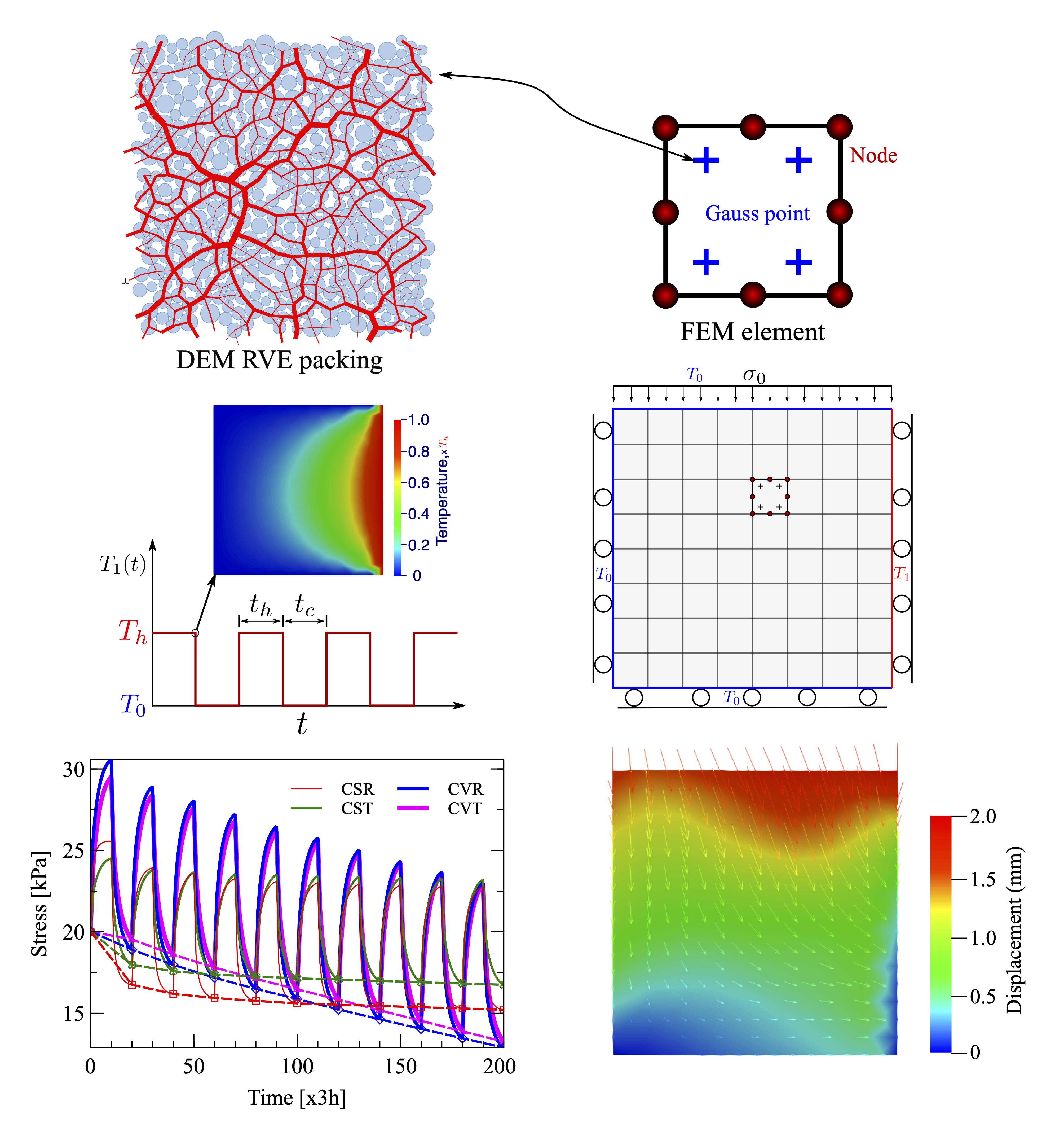
Compaction Front in Granular Rocks
We have further extended the multiscale modeling framework to simulating granular rocks such as sandstone and limestone. We replicated the compaction band in a high-porosity limestone (Tuffeau de Maastricht) observed in X-ray tomography based on coupled 3D FEM/DEM simulations, We confirmed that significant debonding accompanied by collapse of macropores and grain rearrangements may constitute the major microstructural mechanisms causing the formation of compaction bands in high-porosity Tuffeau de Maastricht (Read paper).
We have further performed coupled hydromechanical simulation to show that excess pore pressure can result in transitional evolution of deformation band patterns in saturated sandstone, e.g., from compaction band to shear band as shown above. Read our paper published in Engineering Geology.
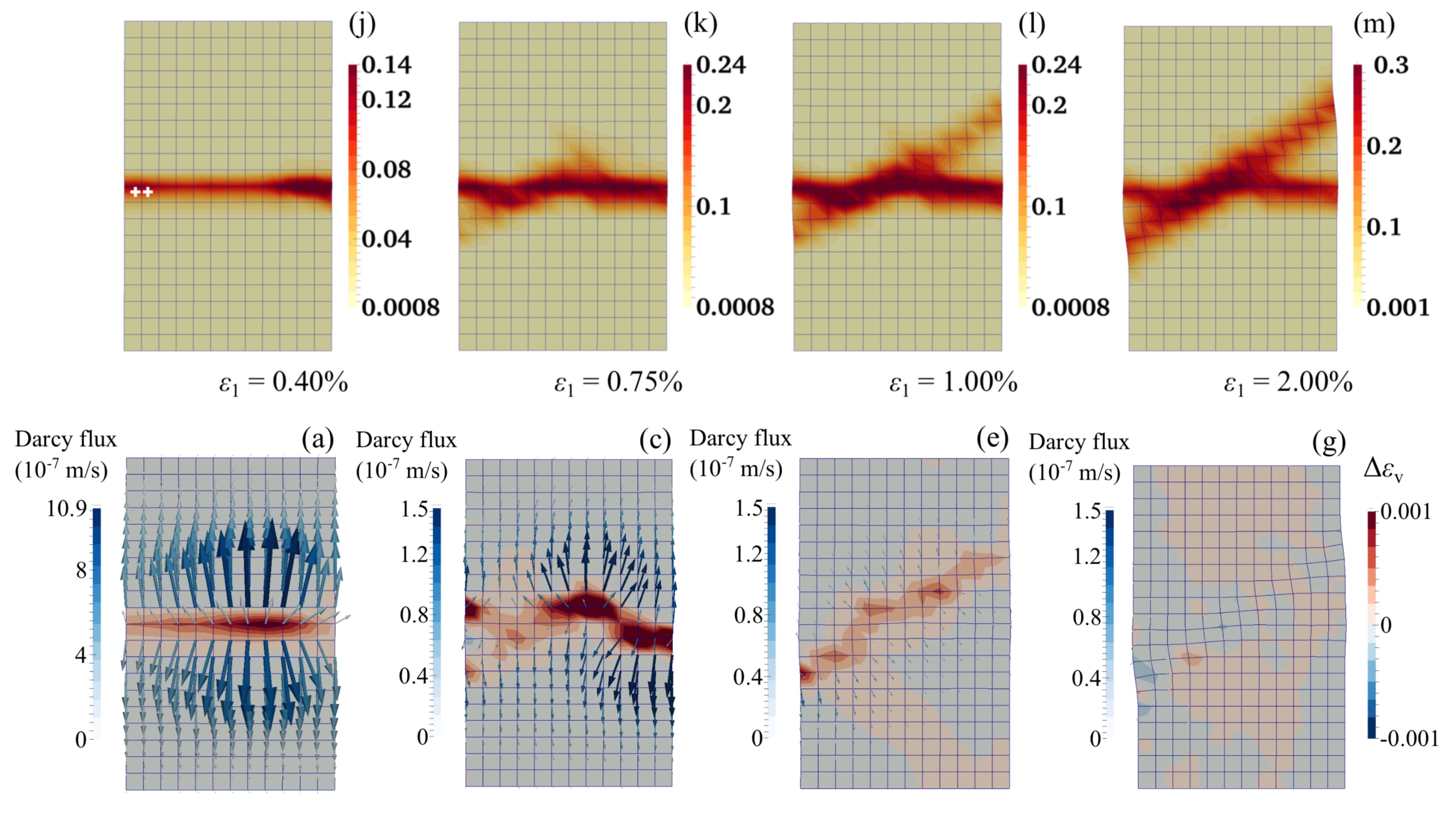
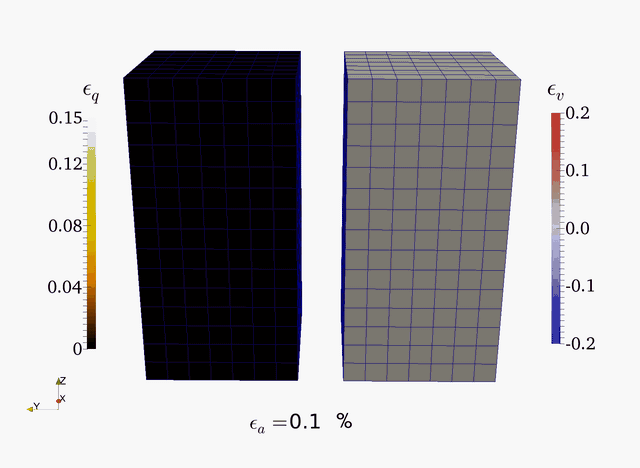

Constitutive Modeling of Granular Sand
(To be updated) We focus on anisotropic critical state of granular soils and develop advanced constitutive models centered on the use of fabric tensor and fabric evaluation to describe both quasi-static and cyclic behavior of granular sand.